Smart Factories: AI Transforming the Manufacturing Landscape
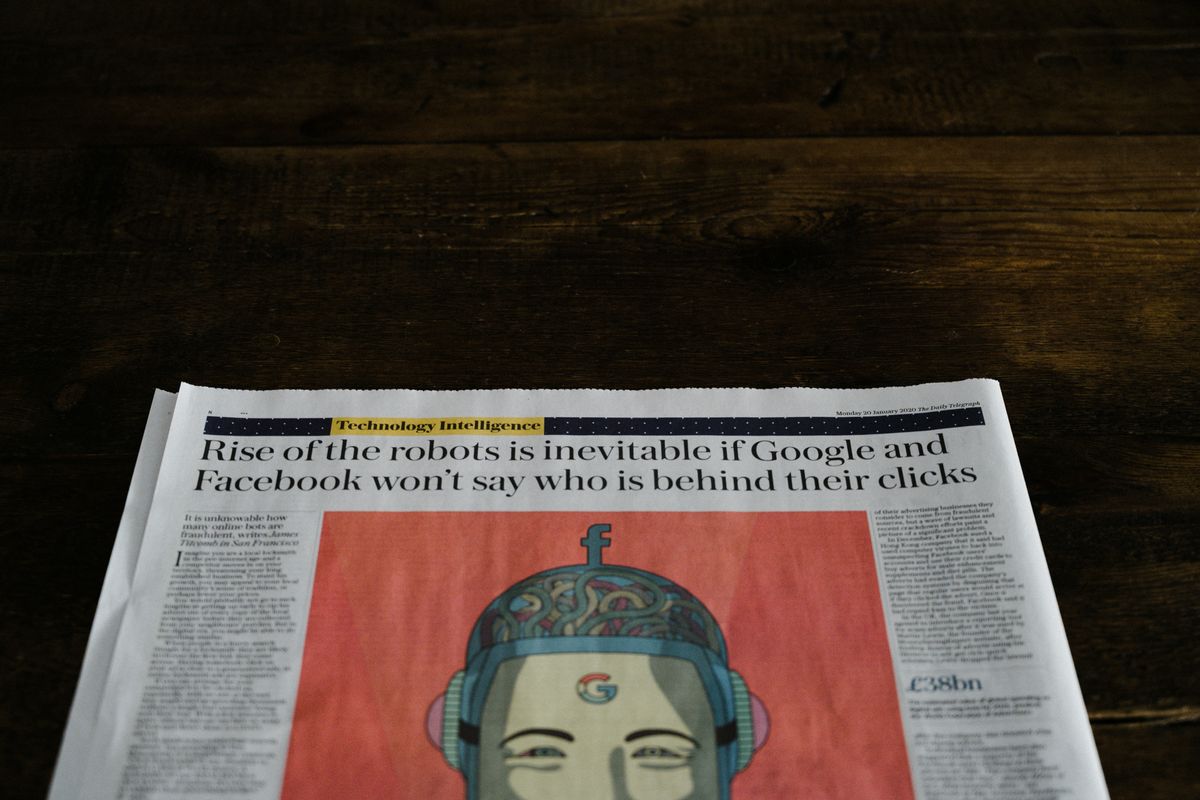
Smart factories are revolutionizing the manufacturing industry through the integration of artificial intelligence technologies. This article explores the various ways AI is transforming the manufacturing landscape, from enhancing automation processes to improving supply chain management.
Key Takeaways
- AI plays a crucial role in enhancing automation processes in smart factories.
- Optimizing production efficiency is a key benefit of implementing AI in manufacturing.
- Predictive maintenance is significantly improved with the use of AI technologies.
- AI-powered quality control enhances defect detection and product inspection in manufacturing.
- AI-driven supply chain management leads to better inventory management, logistics operations, and demand forecasting.
The Role of AI in Smart Factories

Enhancing Automation Processes
The integration of AI into automation processes is revolutionizing the manufacturing industry. AI algorithms are now capable of controlling and optimizing the operations of machinery with minimal human intervention. This not only increases the speed and efficiency of production but also significantly reduces the likelihood of errors.
Robotic Process Automation (RPA) is a key component in this transformation. RPA systems can learn and adapt to new tasks over time, improving their performance and flexibility. The following list outlines the core benefits of AI-enhanced automation:
- Reduction in operational costs
- Increased production speed
- Higher precision and consistency
- Enhanced safety for human workers
By leveraging AI, factories are able to achieve a level of automation that was previously unattainable. This leads to a more streamlined manufacturing process that can quickly respond to market demands and changes in production requirements.
Optimizing Production Efficiency
In the realm of smart factories, optimizing production efficiency is paramount. By leveraging artificial intelligence (AI), manufacturers can streamline their operations, reduce waste, and enhance the overall productivity of their production lines. AI systems analyze vast amounts of data to identify patterns and insights that humans might overlook, enabling more informed decision-making.
- AI-driven algorithms adjust machine settings in real time for optimal performance.
- Predictive analytics forecast production needs, minimizing downtime.
- Intelligent scheduling tools allocate resources effectively, improving throughput.
The integration of AI into production processes marks a significant shift towards more dynamic and responsive manufacturing environments. It is not just about doing things faster; it's about doing them smarter.
The benefits of such optimization are clear. Manufacturers that adopt AI technologies report measurable improvements in production speed, consistency, and adaptability. The table below illustrates the impact of AI on key production metrics:
Metric | Before AI | After AI |
---|---|---|
Production Time | 100% | Reduced by 20% |
Defect Rate | 5% | Reduced to 2% |
Energy Consumption | 100% | Reduced by 15% |
By using these intelligently, companies can optimize their manufacturing processes, leading to increased efficiency, flexibility, and quality improvement.
Improving Predictive Maintenance
Predictive maintenance is revolutionizing the way manufacturers approach equipment upkeep. By leveraging AI, factories can predict failures before they occur, ensuring a proactive rather than reactive maintenance strategy. This shift is critical in minimizing downtime and maintaining a seamless production line.
Predictive analytics play a pivotal role in this process, analyzing vast amounts of data to identify patterns that precede equipment malfunctions. The implementation of such systems can lead to significant cost savings and efficiency gains. For instance, consider the following benefits:
- Reduction in unplanned downtime
- Extension of machinery life
- Decrease in maintenance costs
- Improvement in safety conditions
By adopting predictive maintenance, manufacturers can optimize their maintenance schedules, focusing on the most critical issues and avoiding unnecessary checks.
The integration of AI into maintenance routines is not just about preventing failures; it's about optimizing the entire lifecycle of manufacturing equipment. With the right AI tools, factories are set to become more reliable, efficient, and productive.
AI-Powered Quality Control in Manufacturing
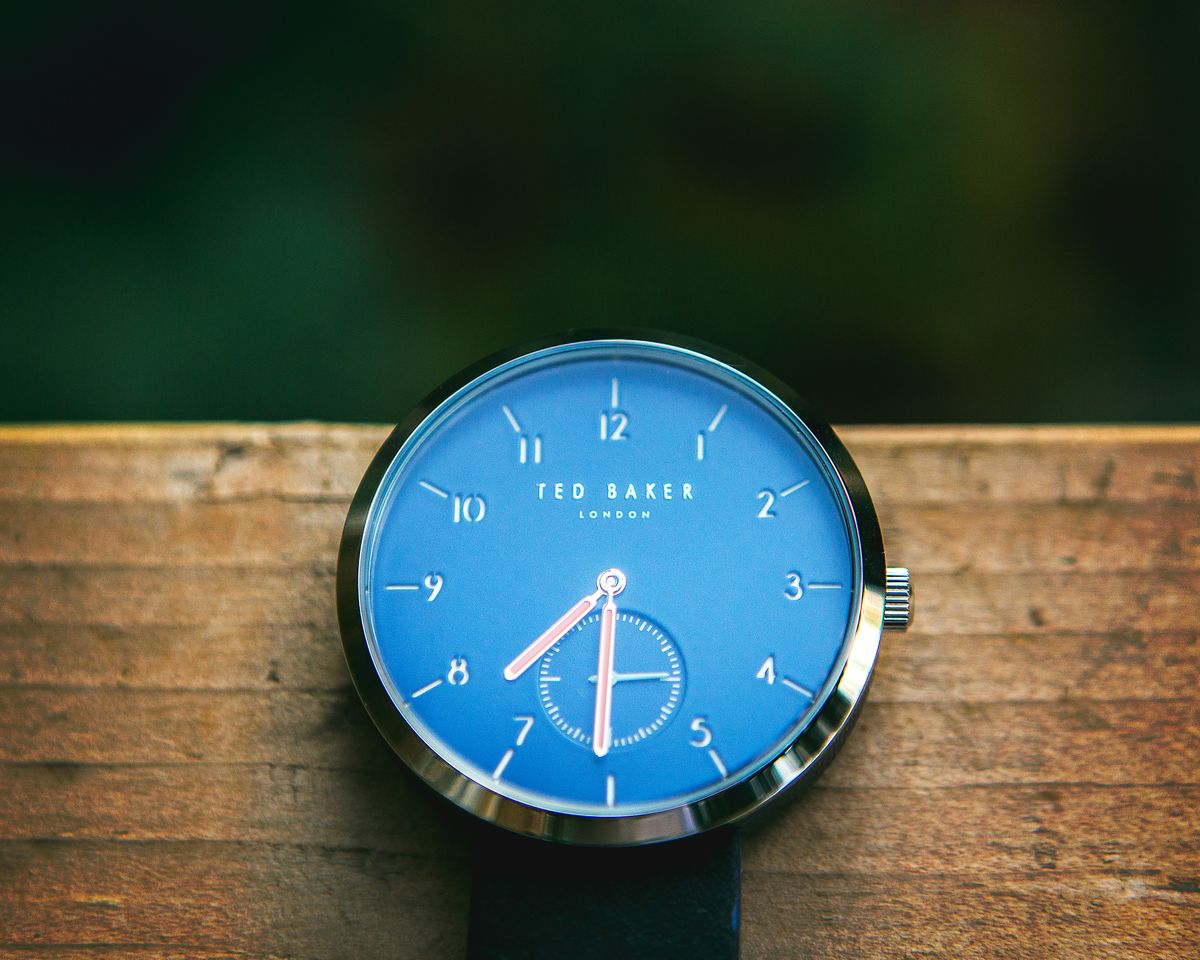
Implementing AI for Defect Detection
The integration of Artificial Intelligence (AI) in manufacturing has revolutionized the approach to defect detection. Automated visual inspection systems, powered by deep learning (DL) models, are now capable of identifying surface defects with unprecedented accuracy and speed. These systems analyze images of products on the production line, comparing them to a dataset of defect-free items to spot any irregularities.
Quality control personnel can now rely on AI to flag potential issues, allowing for immediate correction and reducing the need for costly recalls. This not only ensures a higher standard of product quality but also significantly reduces waste.
- Initial setup of AI models involves training with thousands of images.
- Continuous learning allows the system to improve over time.
- Real-time detection enables on-the-fly adjustments to the production process.
By leveraging AI for defect detection, manufacturers are able to maintain a competitive edge through enhanced quality assurance and resource optimization.
Enhancing Product Inspection
The integration of AI in product inspection has revolutionized the way manufacturers ensure the quality of their products. Deep learning algorithms are now at the forefront of identifying imperfections that might be invisible to the human eye. By training these systems on vast datasets, they learn to recognize a wide range of defects with remarkable accuracy.
Quality control personnel can now rely on AI to provide consistent and objective assessments, reducing the likelihood of human error. This shift not only improves the overall product quality but also significantly speeds up the inspection process. Here's how AI is enhancing product inspection:
- Automated visual inspection systems detect anomalies and classify them based on severity.
- AI algorithms adapt to new products and inspection criteria with minimal human intervention.
- Continuous learning from inspection data leads to ongoing improvement in defect recognition.
The use of AI in product inspection is a testament to the technology's ability to adapt and improve over time, ensuring that manufacturers can maintain high-quality standards in an ever-evolving market.
Ensuring Consistent Quality Standards
In the realm of manufacturing, the integration of AI into quality control systems has been pivotal in ensuring consistent quality standards. By leveraging advanced algorithms, manufacturers are able to maintain a uniform level of quality across all products. This consistency is crucial for customer satisfaction and brand reputation.
Smart quality control systems, powered by AI, are not just about detecting defects; they are about creating a culture of excellence. These systems learn over time, adapting to new standards and expectations, thereby continuously improving the quality of the manufacturing output.
- Automated feedback loops for continuous improvement
- Real-time monitoring and adjustments
- Data-driven insights for quality assurance
The goal is to minimize human error and maximize product reliability. By doing so, manufacturers can deliver products that meet both regulatory requirements and consumer expectations.
The table below illustrates the impact of AI on quality control in a manufacturing setting:
Metric | Before AI | After AI |
---|---|---|
Defect Rate | 5% | 1% |
Inspection Time | 30 min | 5 min |
Cost of Quality | High | Reduced |
AI-driven quality control is not just a technological upgrade; it's a strategic imperative for manufacturers aiming to thrive in a competitive market.
AI-Driven Supply Chain Management
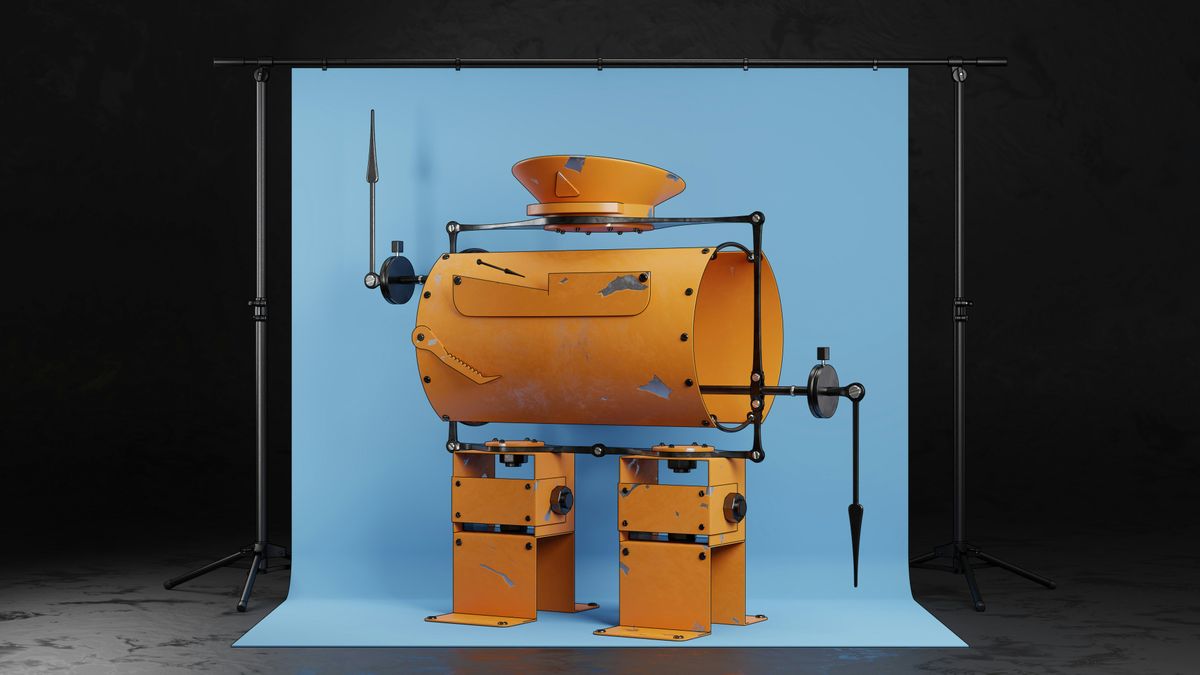
Enhancing Inventory Management
The integration of AI in inventory management has led to significant advancements in how manufacturers monitor and control stock levels. AI systems can predict fluctuations in demand with high accuracy, enabling businesses to maintain optimal inventory levels at all times. This not only reduces the risk of stockouts or overstocking but also minimizes storage costs.
Real-time tracking of inventory using AI algorithms offers unparalleled visibility into the supply chain. Manufacturers can now instantly identify the location and quantity of goods, which is crucial for responding to market changes swiftly.
- Improved stock level optimization
- Enhanced visibility and tracking
- Reduced storage and wastage costs
By leveraging AI, manufacturers are now able to make more informed decisions, leading to a more efficient and responsive supply chain.
The AI revolution in inventory management is a testament to how AI revolutionizes industries, fostering innovation and reshaping economies.
Optimizing Logistics Operations
In the realm of smart factories, the optimization of logistics operations is pivotal for maintaining a competitive edge. AI-driven logistics solutions are revolutionizing the way products are moved and managed, leading to significant cost reductions and improved delivery times. By leveraging predictive analytics, AI can forecast demand and optimize routes, ensuring that goods are delivered in the most efficient manner.
- Real-time tracking of shipments
- Automated route optimization
- Dynamic scheduling of deliveries
The integration of AI into logistics operations not only enhances efficiency but also increases the adaptability of the supply chain to unforeseen events.
The table below illustrates the impact of AI on key logistics metrics:
Metric | Before AI | After AI |
---|---|---|
Delivery Time | 5 days | 3 days |
Cost per Shipment | $100 | $70 |
Accuracy of Delivery | 90% | 98% |
Embracing AI in logistics operations is not just about technology; it's about reimagining the entire supply chain process to meet the demands of a rapidly changing world.
Improving Demand Forecasting
The integration of AI in demand forecasting has revolutionized the way manufacturers anticipate market needs. By analyzing vast amounts of data, AI algorithms can predict product demand with remarkable accuracy. This foresight enables manufacturers to adjust production schedules, manage inventory levels, and optimize resource allocation.
AI-driven demand forecasting is particularly effective when paired with human expertise. Our framework for customized demand forecasting provides a structured approach based on two factors: product life cycle and demand volatility. Based on this, manufacturers can fine-tune their strategies to meet market demands more precisely.
The synergy between AI models and human intuition creates a robust demand forecasting system that adapts to changing market conditions swiftly and efficiently.
To illustrate the impact of AI on demand forecasting, consider the following benefits:
- Reduction in overstock and stockouts: By predicting demand more accurately, companies can maintain optimal inventory levels.
- Enhanced responsiveness to market trends: AI tools can detect shifts in consumer behavior, allowing companies to react quickly.
- Improved financial performance: Better forecasting leads to cost savings and increased revenue through more strategic decision-making.
Conclusion
In conclusion, the integration of AI technologies in smart factories is revolutionizing the manufacturing landscape. From predictive maintenance to optimized production processes, AI is enhancing efficiency, productivity, and quality in manufacturing operations. As industries continue to embrace AI-driven solutions, the future of manufacturing looks promising with smart factories leading the way towards a more automated and intelligent industry.
Frequently Asked Questions
What is the significance of AI in smart factories?
AI plays a crucial role in enhancing automation processes, optimizing production efficiency, and improving predictive maintenance in manufacturing operations.
How does AI contribute to quality control in manufacturing?
AI is used to implement defect detection, enhance product inspection, and ensure consistent quality standards in manufacturing processes.
In what ways does AI drive supply chain management in manufacturing?
AI enhances inventory management, optimizes logistics operations, and improves demand forecasting in the manufacturing supply chain.
What are the benefits of implementing AI in smart factories?
Implementing AI in smart factories leads to increased productivity, reduced downtime, improved product quality, and better decision-making based on data-driven insights.
How can AI help in reducing maintenance costs in manufacturing facilities?
AI enables predictive maintenance by analyzing data to identify potential issues before they occur, reducing maintenance costs and minimizing unplanned downtime.
What challenges may arise when integrating AI into manufacturing processes?
Challenges may include data privacy concerns, workforce reskilling requirements, integration with existing systems, and the need for continuous monitoring and optimization of AI algorithms.