Precision Production: The Impact of AI on Manufacturing
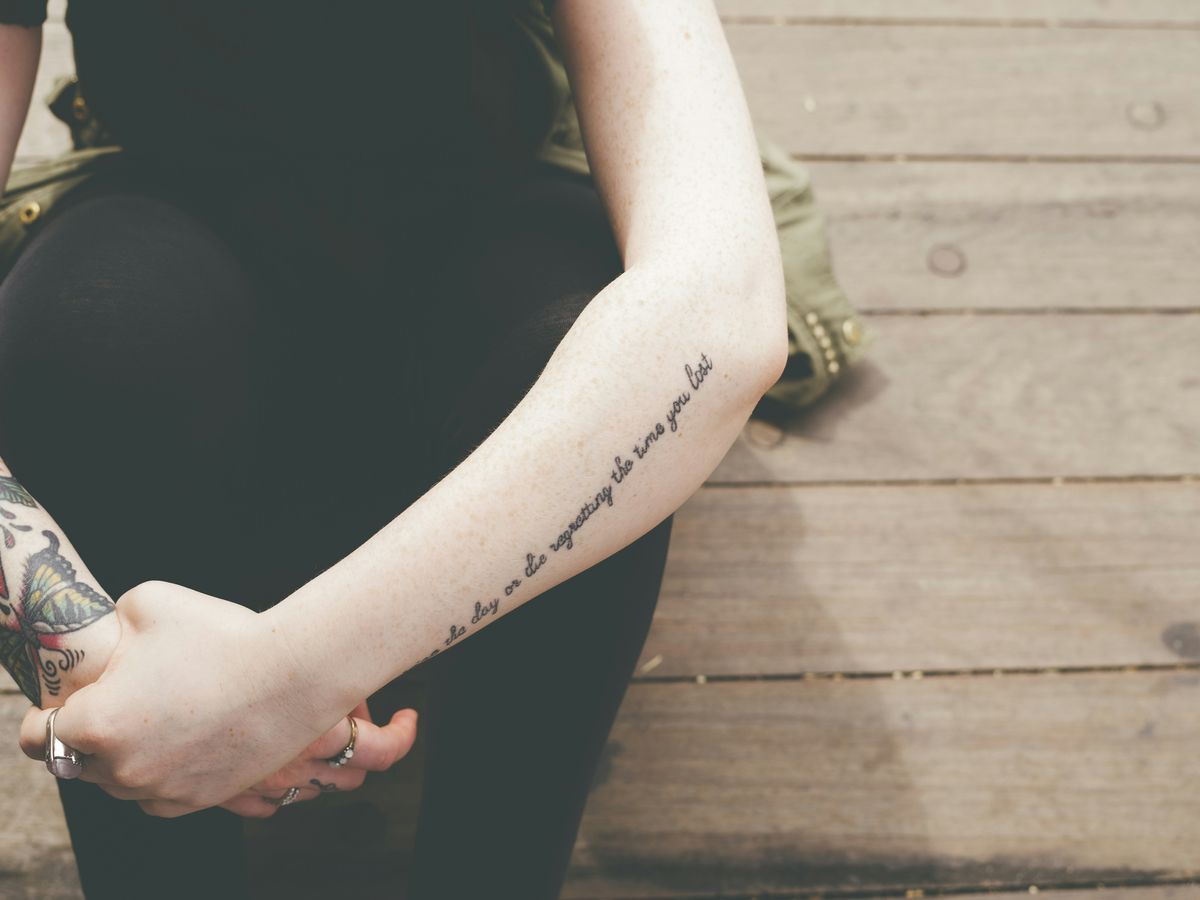
The advent of Artificial Intelligence (AI) has revolutionized the manufacturing industry, bringing about significant changes in production processes and operations. This article explores the role of AI in modern manufacturing, the impact of AI-powered automation on production processes, and the challenges and opportunities of AI integration in the manufacturing sector.
Key Takeaways
- AI enhances production efficiency by automating repetitive tasks and optimizing processes.
- AI improves quality control by detecting defects and anomalies in real-time, leading to higher product quality.
- AI optimizes supply chain management by forecasting demand, reducing lead times, and enhancing overall efficiency.
- AI-powered automation streamlines assembly lines, leading to increased productivity and reduced operational costs.
- Challenges of AI integration in manufacturing include data security concerns, the need for skill development among the workforce, and adapting to Industry 4.0 standards.
The Role of AI in Modern Manufacturing
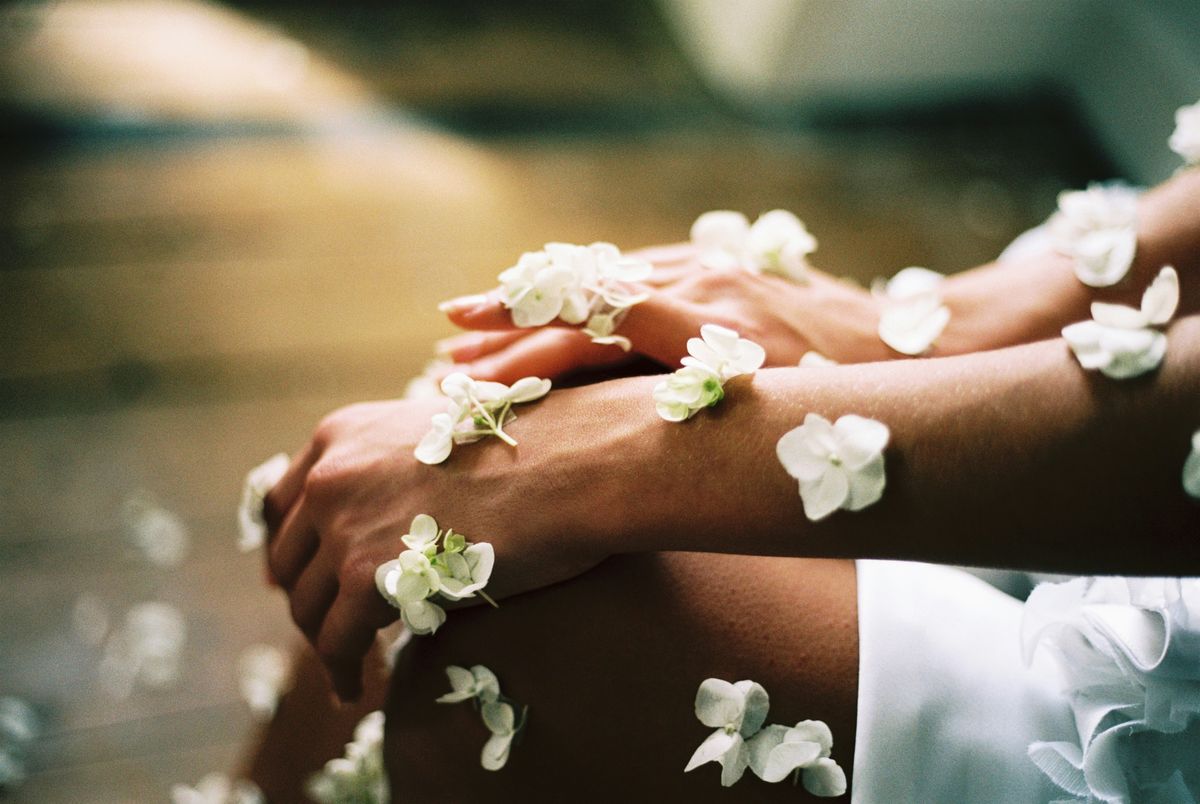
Enhancing Production Efficiency
The integration of Artificial Intelligence (AI) into manufacturing has revolutionized the way factories operate. AI for manufacturing can significantly boost efficiency by optimizing the coordination of production processes. This ensures that each aspect of manufacturing is functioning at its peak, leading to a more streamlined operation.
Efficiency in manufacturing is not just about speed; it's about making smart decisions. AI systems analyze vast amounts of data to identify patterns and predict outcomes, enabling manufacturers to make informed decisions quickly. This can lead to reductions in downtime and waste, while increasing output and quality.
- Real-time monitoring of equipment performance
- Adaptive control systems for process optimization
- Predictive analytics for demand forecasting
By leveraging AI, manufacturers are able to respond more rapidly to changes in demand, adjust production schedules on the fly, and minimize inefficiencies across their operations.
The table below illustrates the impact of AI on key production metrics:
Metric | Before AI | After AI |
---|---|---|
Downtime | 10% | 5% |
Output | 100 units/hr | 150 units/hr |
Waste | 5% | 2% |
The data highlights the tangible benefits of AI in enhancing production efficiency, with significant improvements in downtime, output, and waste reduction.
Improving Quality Control
The integration of AI in quality control processes has revolutionized the way manufacturers detect and address defects. AI-driven systems are now capable of analyzing vast amounts of data from production lines, identifying patterns that may indicate quality issues. This proactive approach allows for immediate corrections, significantly reducing the incidence of defective products reaching the customer.
Machine vision, combined with AI algorithms, has become a cornerstone in maintaining high-quality standards. These systems provide real-time feedback to operators, ensuring that any deviations from the norm are caught and rectified swiftly. The result is a more consistent product quality and a reduction in waste.
The synergy of AI and machine vision empowers manufacturers to enhance product quality, reduce defects, and maintain high levels of efficiency.
The benefits of AI in quality control can be summarized in the following points:
- Precise detection of anomalies and defects
- Real-time monitoring and feedback mechanisms
- Data-driven insights for continuous improvement
- Reduced downtime due to fewer quality issues
Optimizing Supply Chain Management
The integration of AI into supply chain management has revolutionized the way manufacturers approach logistics and inventory control. AI-driven analytics provide deep insights into demand forecasting, enabling businesses to adjust their production schedules and inventory levels with unprecedented precision. This not only reduces waste but also ensures that products are available when and where they are needed.
Supply chain visibility is greatly enhanced through AI, allowing for real-time tracking of materials and products from the supplier to the end customer. This transparency is crucial for identifying bottlenecks and improving the overall flow of goods. Moreover, AI can help improve supplier relationship management (SRM) by making it more consistent and efficient, which is essential for maintaining a resilient supply chain.
By leveraging AI, companies can achieve a more agile and responsive supply chain, which is vital in today's fast-paced market.
The following table highlights the impact of AI on key supply chain management aspects:
Aspect | Impact of AI |
---|---|
Demand Forecasting | Enhanced accuracy |
Inventory Management | Reduced waste, optimized stock levels |
Logistics | Improved routing and delivery times |
SRM | Streamlined processes, better selection |
Embracing AI in supply chain management not only streamlines operations but also opens up new opportunities for growth and innovation.
AI-Powered Automation in Manufacturing Processes
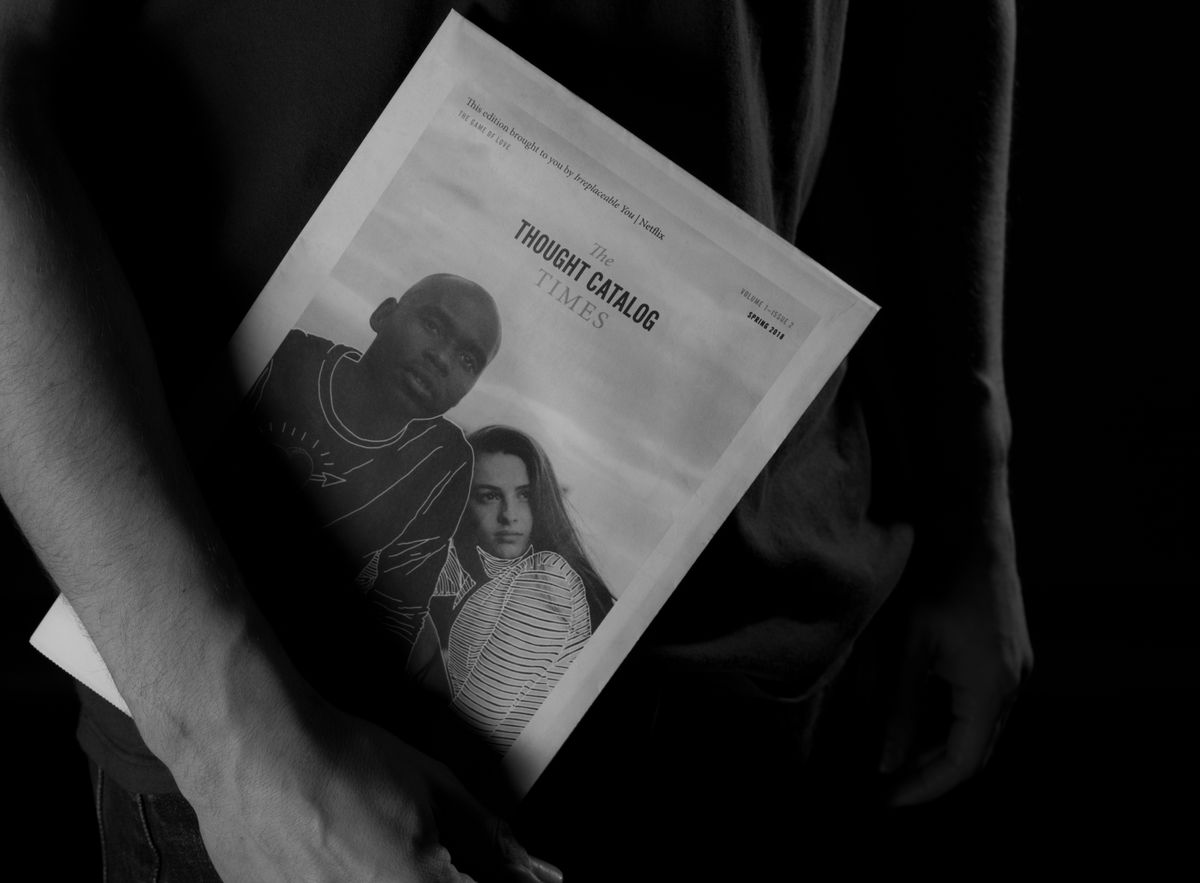
Streamlining Assembly Lines
The integration of AI into assembly lines is revolutionizing the way manufacturers approach production. AI-driven automation is not just about replacing human labor; it's about creating a more synchronized manufacturing environment. By analyzing vast amounts of data, AI systems can optimize the workflow, reducing bottlenecks and enhancing overall efficiency.
- Predictive analytics enable real-time adjustments to the production process.
- Intelligent robots can work alongside humans, learning and adapting to new tasks.
- Automated quality checks ensure consistent product standards.
The goal is to achieve a seamless flow of operations, where each component of the assembly line communicates and operates in harmony. This not only speeds up production but also reduces errors and waste, contributing to a leaner manufacturing process.
The impact of AI on assembly lines can be seen in the significant improvements in production planning. Enhanced production planning through AI systems can predict demand, optimize inventory levels, and streamline production schedules, ensuring efficient resource utilization and minimizing downtime.
Predictive Maintenance Strategies
The advent of AI in manufacturing has revolutionized the approach to maintenance. Predictive maintenance strategies, powered by AI algorithms, enable manufacturers to anticipate equipment failures before they occur. This proactive stance is critical in minimizing downtime and maintaining a seamless production flow.
Predictive maintenance harnesses machine learning to analyze data from sensors and logs, identifying patterns that precede equipment issues. By doing so, it shifts the maintenance paradigm from a reactive to a proactive one, significantly reducing the risk of unexpected breakdowns and the costs associated with them.
- Early fault detection: Identifying potential problems before they escalate.
- Maintenance scheduling: Planning interventions at the most opportune times.
- Resource optimization: Allocating maintenance resources more efficiently.
- Extended equipment life: Preventing severe damage through timely maintenance.
Predictive maintenance is the key to forecast when machine maintenance will be required, rather than reacting to an unplanned outage, saves time and money.
Customized Product Development
The advent of AI in manufacturing has paved the way for mass customization, a concept that allows for high variability in products without sacrificing efficiency. AI systems can analyze customer data to predict trends and preferences, enabling manufacturers to create personalized products at scale. This approach not only meets the individual needs of customers but also gives companies a competitive edge.
- Understanding customer preferences
- Tailoring products to specific needs
- Maintaining production efficiency
The process of integrating AI into product development requires careful planning and execution. Manufacturers must balance the desire for customization with the practicalities of production processes and costs. However, the benefits of this strategy are clear, as it leads to higher customer satisfaction and loyalty.
The realm of mass customization opens up a plethora of opportunities for manufacturers, offering a strategic avenue to differentiate products from competitors.
Challenges and Opportunities of AI Integration in Manufacturing
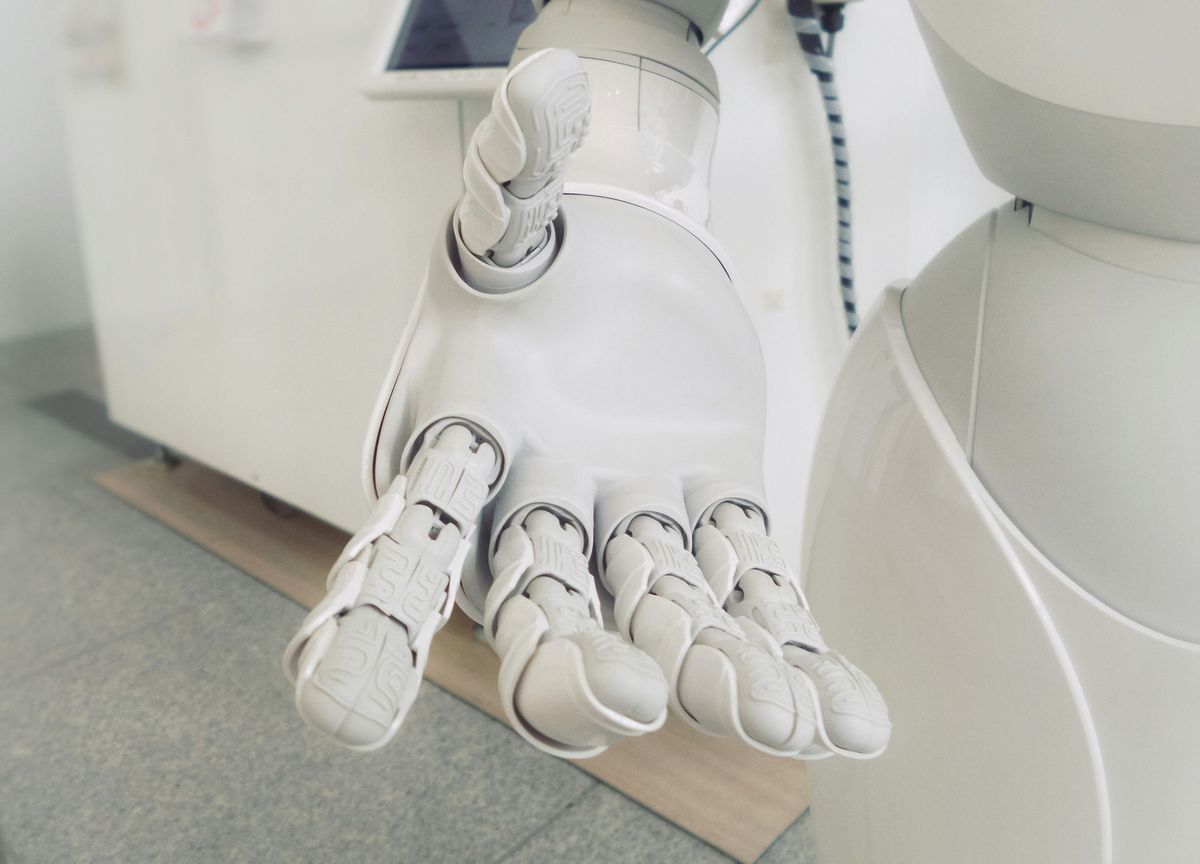
Data Security Concerns
As manufacturing companies integrate more AI and IoT devices into their operations, the volume of data generated increases exponentially. This data often includes sensitive information about production processes, proprietary technologies, and customer details. Protecting this data from breaches and unauthorized access is paramount, and requires robust security protocols.
Cybersecurity measures must be tailored to the specific needs of the manufacturing sector, taking into account the unique vulnerabilities presented by interconnected systems. A comprehensive approach to data security can include:
- Regular security audits and updates
- Employee training on data handling and phishing awareness
- Implementation of end-to-end encryption for data in transit and at rest
- Deployment of intrusion detection and prevention systems
Ensuring data integrity and confidentiality is not just about preventing financial losses; it's about maintaining trust with customers and upholding the brand's reputation.
The integration of AI in manufacturing also opens up new avenues for cyber-attacks. As such, manufacturers must stay vigilant and continuously update their security measures to keep pace with the evolving threat landscape.
Skill Development for Workforce
The integration of AI in manufacturing necessitates a skilled workforce capable of operating and maintaining sophisticated systems. Upskilling existing employees and educating new entrants are essential to harness the full potential of AI technologies. Training programs must evolve to include AI literacy, ensuring workers are adept at interacting with advanced machinery and software.
Workforce development is not just about technical skills; it also involves cultivating a mindset open to continuous learning and adaptation. The following points highlight the key areas of focus:
- Understanding AI and machine learning basics
- Hands-on experience with AI-powered tools and equipment
- Critical thinking and problem-solving in a high-tech environment
- Collaboration with AI systems and data analysts
Embracing AI requires a cultural shift within the manufacturing sector. Companies must foster an environment where innovation is encouraged, and knowledge sharing is standard practice.
Adapting to Industry 4.0 Standards
The integration of AI into manufacturing is a cornerstone of the Industry 4.0 revolution, demanding a strategic approach to adaptation. Manufacturers must embrace digital transformation to stay competitive, which includes the implementation of smart factories, IoT devices, and real-time data analytics.
To successfully adapt, companies should consider the following steps:
- Assessing current technological infrastructure
- Training employees on new AI systems
- Establishing partnerships with tech providers
- Continuously monitoring and refining AI applications
Embracing AI is not just about adopting new technologies; it's about fostering a culture of innovation and continuous improvement.
As the AI revolutionizes industries, it's imperative for manufacturers to innovate with AI, not only to create new opportunities but also to address the challenges of a rapidly evolving world. The journey towards Industry 4.0 is complex, but with careful planning and execution, it can lead to significant gains in efficiency and productivity.
Conclusion
In conclusion, the integration of AI in manufacturing has revolutionized precision production processes. From predictive maintenance to quality control, AI technologies have significantly improved efficiency, accuracy, and productivity in the manufacturing industry. As manufacturers continue to adopt AI solutions, we can expect further advancements in automation, optimization, and customization. The future of manufacturing is indeed being shaped by the transformative impact of AI, paving the way for smarter, more agile, and competitive production systems.
Frequently Asked Questions
How does AI enhance production efficiency in modern manufacturing?
AI can analyze vast amounts of data in real-time to optimize production processes, identify bottlenecks, and suggest improvements, leading to increased efficiency.
What role does AI play in improving quality control in manufacturing?
AI can detect defects, anomalies, and variations in products with high accuracy, ensuring consistent quality and reducing the likelihood of faulty products reaching the market.
How does AI optimize supply chain management in manufacturing?
AI enables predictive analytics to forecast demand, manage inventory levels efficiently, and streamline logistics, resulting in cost savings and improved supply chain performance.
What are the benefits of streamlining assembly lines with AI-powered automation?
By automating repetitive tasks and optimizing workflows, AI can increase production speed, reduce errors, and enhance overall productivity on assembly lines.
How can predictive maintenance strategies powered by AI benefit manufacturing processes?
AI algorithms can analyze equipment data to predict maintenance needs, schedule repairs proactively, and minimize downtime, ultimately extending the lifespan of machinery and reducing maintenance costs.
In what ways does AI facilitate customized product development in manufacturing?
AI can analyze customer preferences and market trends to create personalized products, optimize design processes, and adapt manufacturing operations to meet individualized demands.