Industry 4.0: Revolutionizing Manufacturing with Artificial Intelligence
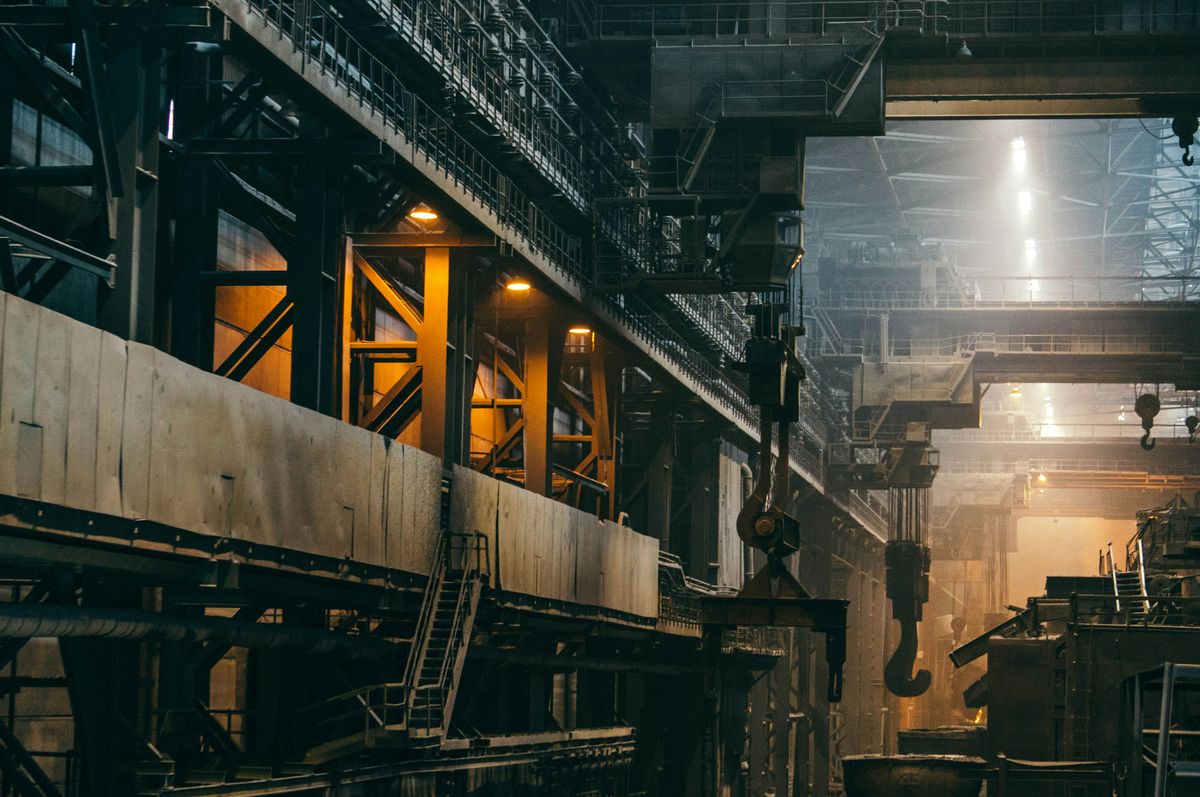
In the era of Industry 4.0, the integration of Artificial Intelligence (AI) has revolutionized the manufacturing sector, leading to increased efficiency, automation, and predictive capabilities. This article explores the role of AI in Industry 4.0, the challenges and opportunities in implementing AI in manufacturing, and the impact of AI on supply chain management.
Key Takeaways
- Artificial Intelligence enhances automation processes in manufacturing.
- Optimizing production efficiency through AI implementation is crucial for Industry 4.0.
- Predictive maintenance powered by AI technology improves equipment reliability and reduces downtime.
- Data security concerns must be addressed when implementing AI in manufacturing.
- Closing the skill gap in the workforce is essential for successful AI integration in manufacturing.
The Role of Artificial Intelligence in Industry 4.0
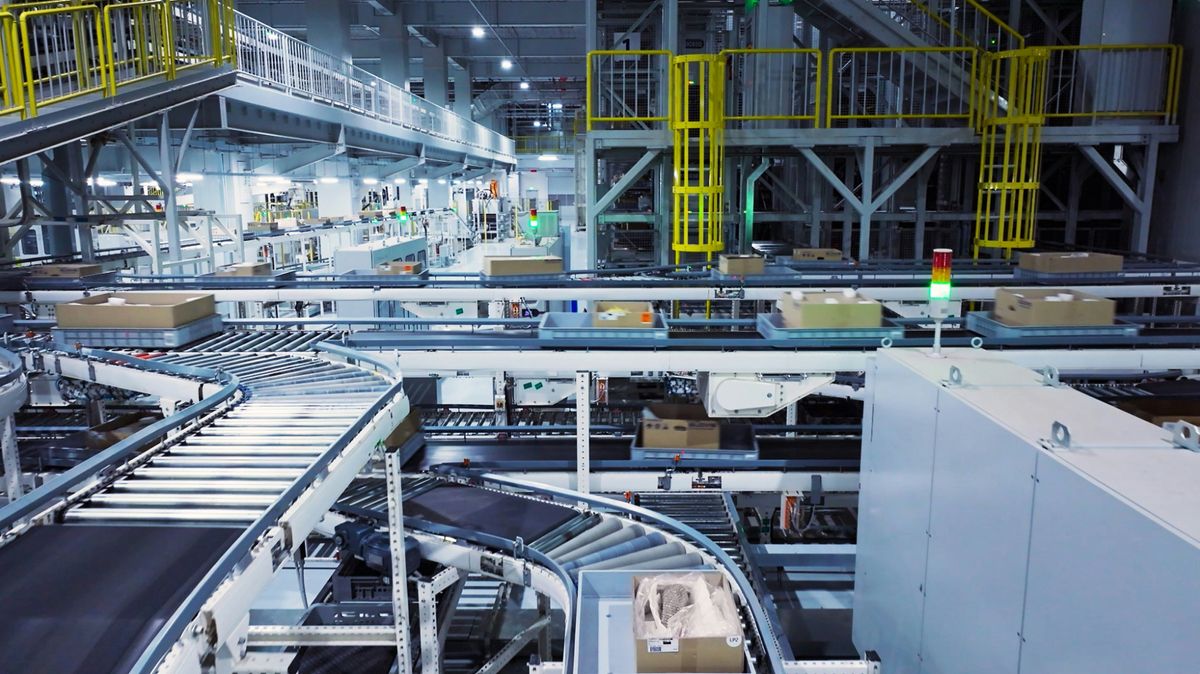
Enhancing Automation Processes
The integration of Artificial Intelligence (AI) into automation processes is a cornerstone of Industry 4.0. AI-driven systems are transforming the manufacturing landscape by enabling machines to make decisions and carry out tasks with minimal human intervention. This shift not only increases the speed and accuracy of production but also allows for more complex operations to be automated.
Flexibility is a key advantage of AI in automation. Unlike traditional automated systems, AI can adapt to changes in the environment or the production process without the need for extensive reprogramming. This adaptability is crucial in today's fast-paced market where consumer demands and production technologies are constantly evolving.
- Improved product quality
- Reduced operational costs
- Enhanced safety
The ability to quickly adjust to new manufacturing requirements and the reduction of downtime are significant benefits that AI brings to automation processes.
By leveraging AI, manufacturers can expect a significant improvement in overall operational efficiency. The technology not only streamlines workflows but also provides valuable insights that can lead to continuous improvement and innovation.
Optimizing Production Efficiency
In the realm of Industry 4.0, optimizing production efficiency is a cornerstone for competitive manufacturing. By leveraging artificial intelligence (AI), companies can analyze vast amounts of data to streamline operations and reduce waste. AI systems can identify patterns and suggest improvements that might be invisible to the human eye, leading to significant cost savings and increased output.
- Real-time monitoring of production lines ensures immediate response to any inefficiencies.
- AI algorithms can predict optimal maintenance schedules, avoiding downtime.
- Advanced analytics provide insights for continuous process improvement.
The integration of AI into manufacturing processes is not just about maintaining efficiency; it's about redefining the benchmarks of productivity and quality.
The table below illustrates the impact of AI on key production metrics:
Metric | Before AI | After AI |
---|---|---|
Output | 100 units | 150 units |
Defect Rate | 5% | 2% |
Downtime | 10 hours | 4 hours |
Embracing AI in manufacturing paves the way for a more agile and responsive production environment. It is essential for businesses to stay ahead in a rapidly evolving market where efficiency is synonymous with survival.
Enabling Predictive Maintenance
The integration of AI into manufacturing has paved the way for predictive maintenance, a game-changing approach that anticipates equipment failures before they occur. By analyzing data from sensors and machines, AI algorithms can identify patterns and anomalies that suggest potential issues, allowing for timely interventions.
Predictive maintenance not only reduces downtime but also extends the lifespan of machinery. This proactive strategy is a stark contrast to traditional reactive maintenance, which only addresses problems after they have arisen. The benefits of this shift are clear:
- Decreased maintenance costs
- Minimized unplanned outages
- Improved equipment reliability
- Enhanced safety for workers
By leveraging AI for predictive maintenance, manufacturers are setting new standards for operational excellence, ensuring that their machinery is always running at peak performance.
The implementation of predictive maintenance is a testament to how AI revolutionizes industries, not just in manufacturing but also in sectors like healthcare, where it enhances efficiency and patient care.
Challenges and Opportunities in Implementing AI in Manufacturing
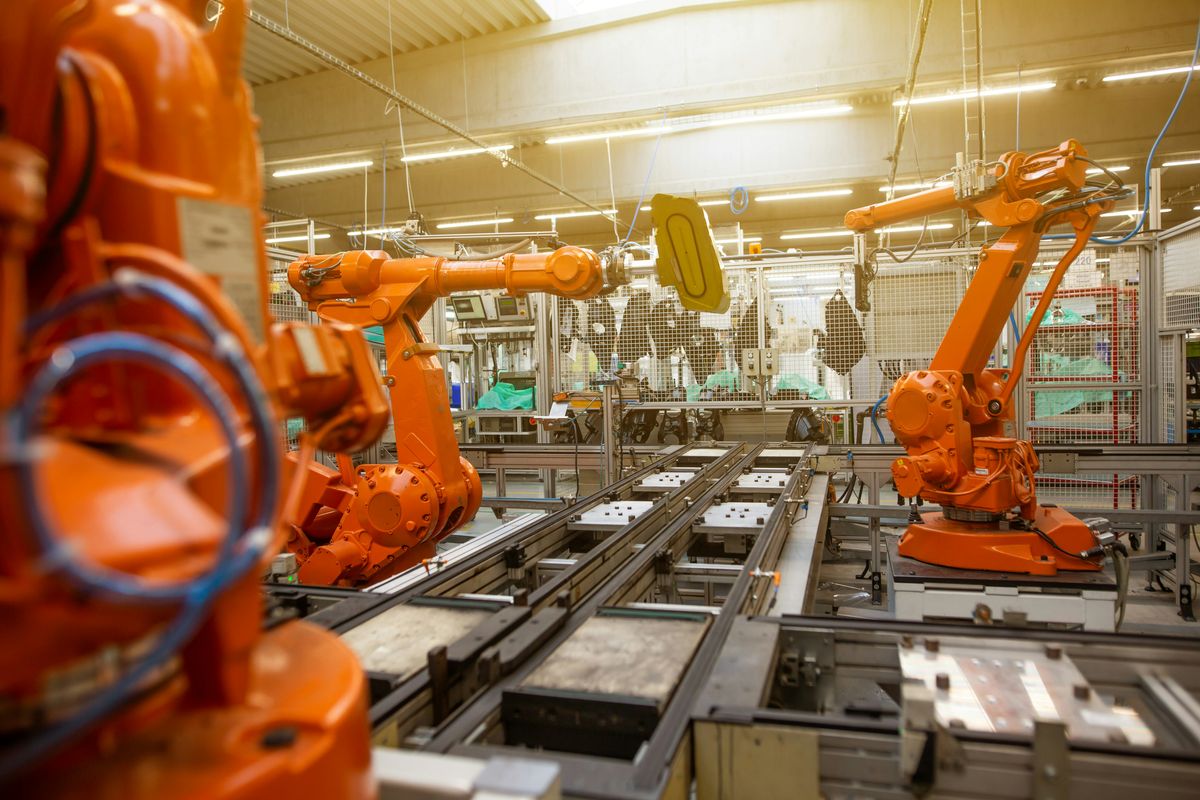
Data Security Concerns
The integration of AI into manufacturing systems introduces significant data security concerns. Protecting sensitive information becomes paramount as more devices connect to the Internet of Things (IoT), creating potential vulnerabilities. Manufacturers must ensure robust cybersecurity measures are in place to safeguard against data breaches and cyber-attacks.
- Assessment of current security infrastructure
- Identification of potential threats
- Development of a comprehensive security strategy
- Regular updates and maintenance of security systems
The effect of IT security issues on the implementation of industry 4.0 is particularly pronounced in SMEs, where resources for extensive cybersecurity may be limited.
It is crucial for manufacturers to not only address these concerns but also to maintain transparency with stakeholders about the steps being taken to protect data. This builds trust and ensures the smooth adoption of AI technologies.
Skill Gap in Workforce
The advent of Industry 4.0 has brought with it a significant skill gap in the manufacturing workforce. As companies increasingly adopt artificial intelligence and other advanced technologies, the demand for skilled workers who can operate, maintain, and improve these systems has surged. The mismatch between the skills required and those available in the job market is a critical issue that needs to be addressed to fully harness the potential of AI in manufacturing.
One of the most alarming projections is the potential for a large number of unfilled jobs. For instance, the manufacturing skills gap in the U.S. could result in 2.1 million unfilled jobs by 2030. This gap not only affects the growth of individual companies but also has broader economic implications.
To bridge this gap, several steps can be taken:
- Developing targeted education and training programs.
- Encouraging partnerships between industry and educational institutions.
- Promoting STEM (Science, Technology, Engineering, and Mathematics) subjects at an early age.
- Providing upskilling and reskilling opportunities for the existing workforce.
It is imperative for industry leaders to invest in workforce development initiatives that can prepare workers for the high-tech manufacturing environment of tomorrow.
Integration with Existing Systems
Integrating AI into existing manufacturing systems is a complex task that often involves bridging the gap between new and legacy technologies. Compatibility issues may arise, as older systems were not designed with AI integration in mind. To ensure a smooth transition, manufacturers must assess their current infrastructure and determine the necessary upgrades or adaptations.
Interoperability is key to successful AI integration. It requires a strategic approach that includes:
- Evaluating the existing hardware and software capabilities
- Identifying the data formats and protocols in use
- Planning for a phased implementation to minimize disruptions
The goal is to create a cohesive environment where AI can effectively communicate with and enhance the existing systems.
By addressing these challenges, manufacturers can unlock the full potential of AI, leading to increased efficiency and a stronger competitive edge in the market.
Impact of AI on Supply Chain Management
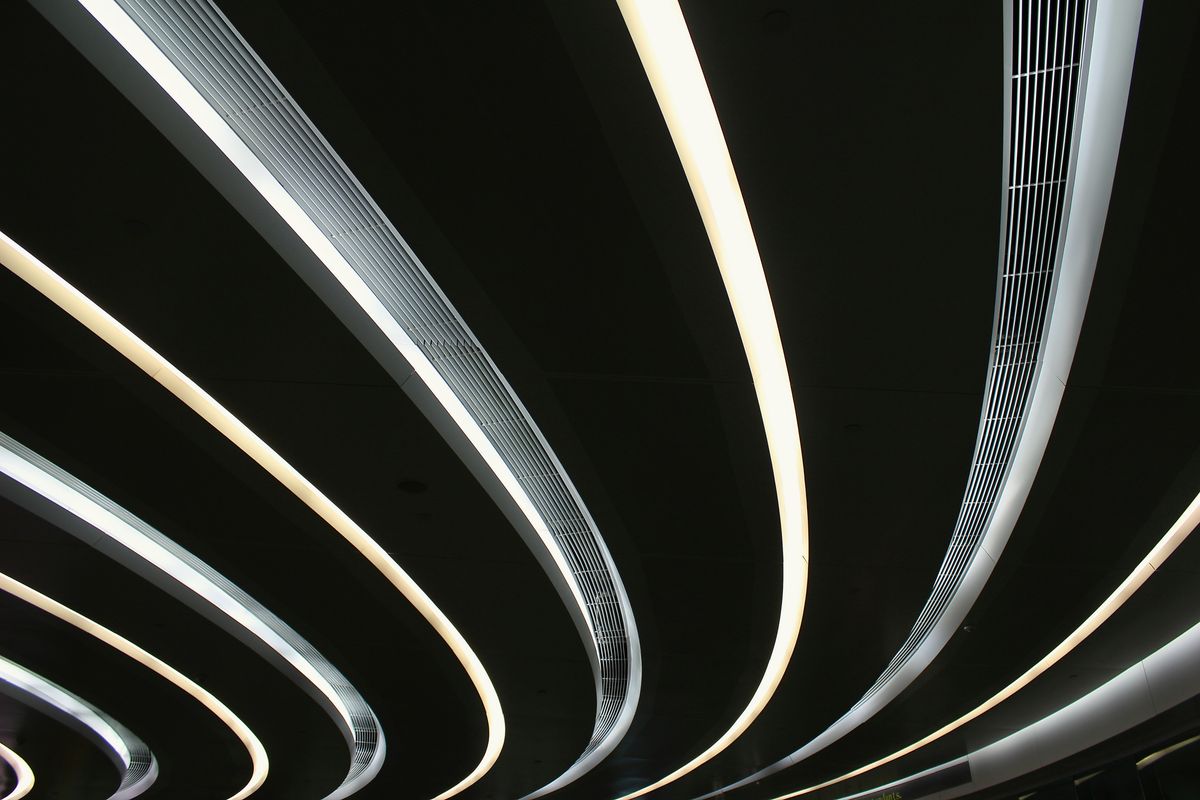
Real-time Inventory Management
The advent of Industry 4.0 has brought about a significant shift in how inventory is managed within the manufacturing sector. Real-time inventory management systems, often powered by technologies such as Real-Time Location Systems (RTLS), are pivotal in maintaining a seamless production flow. By leveraging smart factory capabilities, these systems provide instant visibility into the location and status of inventory, ensuring that materials and components are always available when needed.
The integration of RTLS in Industry 4.0 environments facilitates a proactive approach to inventory control, reducing the risk of stockouts and overstock situations.
This dynamic approach to inventory management not only minimizes delays but also contributes to maximizing overall production efficiency. The table below illustrates the impact of real-time inventory management on key manufacturing metrics:
Metric | Before RTLS | After RTLS |
---|---|---|
Production Delays | Frequent | Rare |
Inventory Accuracy | Low | High |
Order Fulfillment Time | Longer | Reduced |
By keeping a constant eye on inventory levels and movement, manufacturers can respond more swiftly to changes in demand and production requirements, leading to a more agile and responsive manufacturing process.
Demand Forecasting Accuracy
The advent of Industry 4.0 has brought cognitive demand forecasting to the forefront, enabling manufacturers to predict future product demand with unprecedented precision. Accurate demand forecasting is crucial for optimizing inventory levels, reducing waste, and ensuring timely delivery of products.
- By analyzing historical sales data, market trends, and consumer behavior, AI algorithms can identify patterns and predict future demand more accurately than traditional methods.
- This data-driven approach allows for more strategic planning and decision-making, leading to increased operational efficiency and customer satisfaction.
The integration of AI in demand forecasting represents a significant leap towards a more responsive and agile manufacturing sector.
While the benefits are clear, the journey to achieving high forecasting accuracy is not without its challenges. Manufacturers must navigate the complexities of data collection and analysis, and ensure their teams are equipped with the necessary skills to interpret and act on AI-generated insights.
Enhanced Supplier Relationship Management
The advent of Industry 4.0 has brought about a transformative approach to Supplier Relationship Management (SRM). By leveraging AI, companies can now engage in more strategic partnerships with their suppliers, fostering a collaborative environment that benefits all parties involved. AI-driven analytics provide deep insights into supplier performance, enabling businesses to make informed decisions and strengthen their supply chain.
- Improved risk management through predictive analytics
- Enhanced communication via automated systems
- Strategic sourcing based on data-driven insights
The integration of AI into SRM systems has not only streamlined processes but also paved the way for more dynamic and resilient supply chains. With AI, the potential for innovation in supplier interactions is vast, leading to improved efficiency and competitiveness.
Furthermore, the implementation of AI in SRM has led to the development of more procurement-oriented systems, such as e-procurement and e-sourcing, which are revolutionizing the way companies manage their purchasing activities. These systems facilitate a more efficient Purchase to Pay (P2P) process, ensuring that transactions are completed swiftly and with greater accuracy.
Conclusion
In conclusion, Industry 4.0 is transforming the manufacturing sector through the integration of artificial intelligence. This revolution is enhancing efficiency, productivity, and innovation in factories worldwide. As businesses embrace the power of AI, they are poised to stay competitive in the rapidly evolving industrial landscape. The future of manufacturing is indeed being shaped by the advancements in Industry 4.0, paving the way for a new era of smart and interconnected production processes.
Frequently Asked Questions
What is Industry 4.0 and how does it relate to Artificial Intelligence?
Industry 4.0 refers to the fourth industrial revolution characterized by the integration of digital technologies in manufacturing processes. Artificial Intelligence plays a crucial role in Industry 4.0 by enabling machines to learn, adapt, and make decisions autonomously.
How does Artificial Intelligence enhance automation processes in manufacturing?
Artificial Intelligence enhances automation processes by enabling machines to analyze data, identify patterns, and make real-time decisions without human intervention. This leads to increased efficiency, reduced errors, and improved productivity.
What are the key challenges in implementing AI in manufacturing?
Some key challenges include concerns about data security, the skill gap in the workforce to operate AI systems, and the integration of AI with existing manufacturing systems without disrupting operations.
How does AI contribute to real-time inventory management in supply chain management?
AI enables real-time inventory management by analyzing data from sensors, RFID tags, and other sources to track inventory levels accurately. This helps in reducing stockouts, optimizing inventory levels, and improving supply chain efficiency.
Can AI improve demand forecasting accuracy in manufacturing?
Yes, AI can improve demand forecasting accuracy by analyzing historical data, market trends, and external factors to predict future demand more accurately. This leads to better planning, reduced inventory costs, and improved customer satisfaction.
How does AI enhance supplier relationship management in supply chain management?
AI enhances supplier relationship management by analyzing supplier performance data, identifying opportunities for improvement, and predicting supplier behavior. This helps in building stronger partnerships, optimizing procurement processes, and mitigating supply chain risks.