AI in Industrial Goods: Revolutionizing Manufacturing
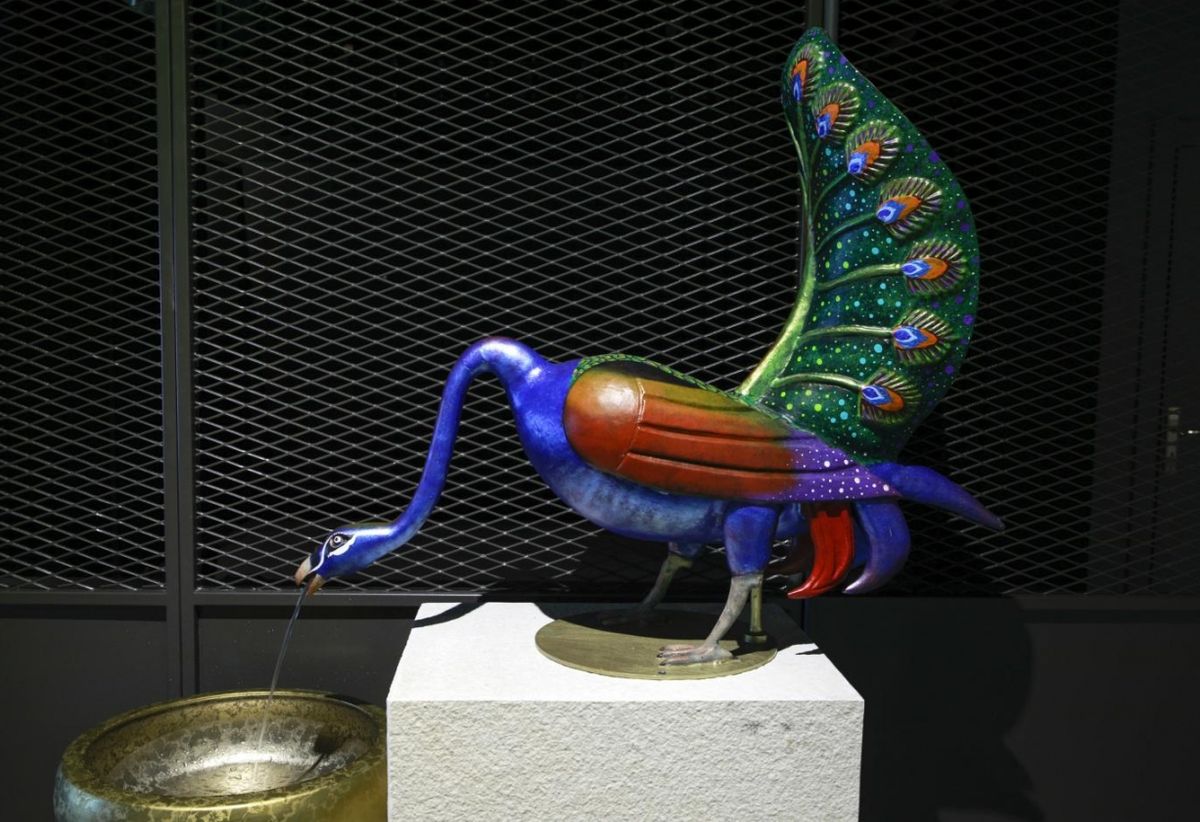
The manufacturing industry is on the cusp of a new era, defined by the integration of Artificial Intelligence (AI). This transformation is characterized by the emergence of smart factories, enhanced efficiency, and improved quality and sustainability. AI-driven technologies are not only automating complex tasks but are also providing real-time analytics, predictive maintenance, and fostering innovation in product development. As we explore the impact of AI on manufacturing, we uncover how it's reshaping the industry, optimizing operations, and setting the stage for the next industrial revolution.
Key Takeaways
- AI is catalyzing a transformative shift in manufacturing, leading to the creation of smart factories with enhanced operational efficiency and reduced costs.
- The implementation of real-time data analytics and AI-driven process optimization is significantly improving production workflows and product quality.
- Through case studies, companies like Siemens and Toyota demonstrate the successful integration of AI in manufacturing, resulting in cost savings and sustainability gains.
- AI is playing a pivotal role in quality control, reducing waste, and driving innovation in product development, leading to more personalized and improved products.
- The future of manufacturing with AI promises adaptability to market changes, evolution in employment, and a readiness for the upcoming industrial revolution.
The Advent of Smart Factories
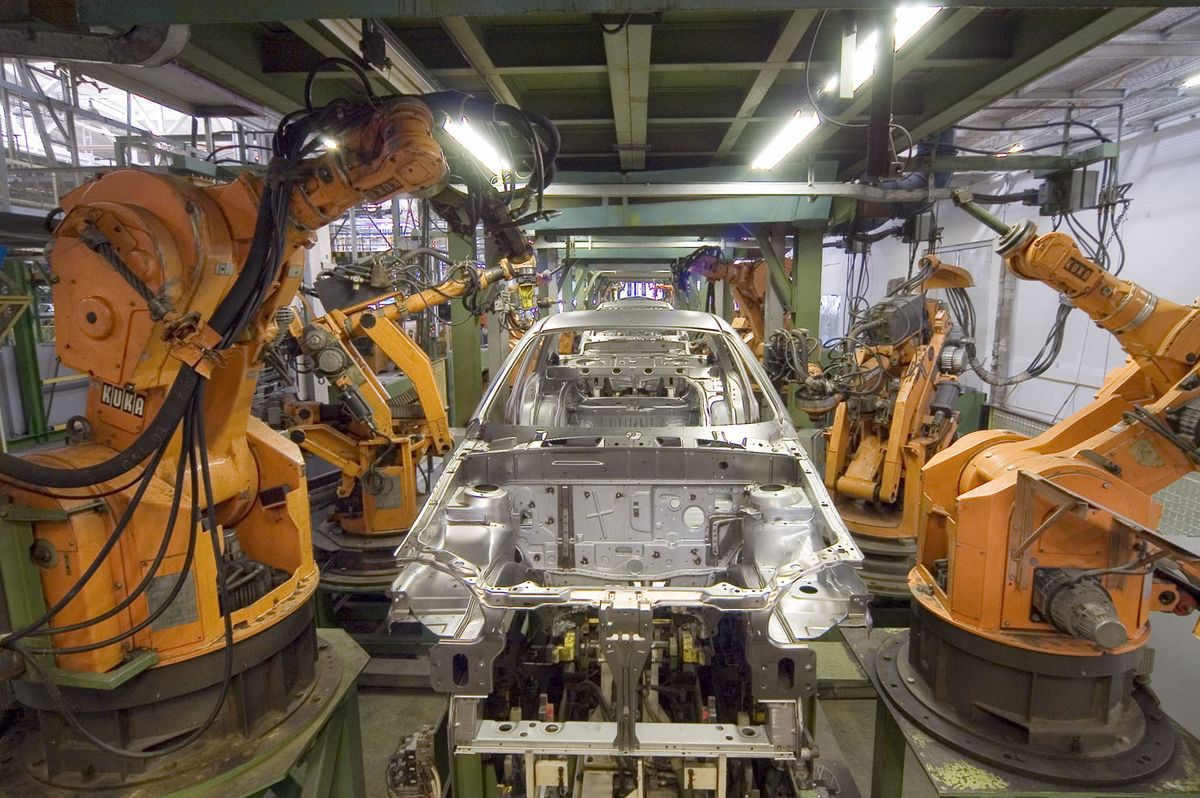
The Role of AI in Modern Manufacturing
The integration of Artificial Intelligence (AI) into manufacturing marks a significant transition towards more efficient and innovative production. AI in smart factories is not merely augmenting existing practices but is fundamentally transforming them. Smart factories equipped with AI are leading the charge in revolutionizing operations, enhancing quality control, and driving product innovation.
Predictive maintenance, intelligent automation, and AI-powered data analytics are just a few examples of how AI is redefining the manufacturing landscape. These technologies enable manufacturers to gain insights and oversee production processes with unprecedented precision.
- Enhanced automation
- Production efficiency
- Predictive maintenance
- Improved supply chain management
- Superior quality control
AI isn't replacing human roles but is complementing human skills, allowing workers to focus on more complex and creative aspects of production.
As we continue to explore the impact of AI, it's clear that its applications in manufacturing are vast and transformative. Companies like Siemens, General Electric, and Toyota are just a few that have harnessed AI to achieve cost savings, quality improvements, and environmental benefits.
Real-time Data Analytics and Process Optimization
In the realm of industrial goods, the integration of AI into manufacturing processes has been a game-changer. Real-time data analytics enable factories to become more responsive and agile. By harnessing the power of AI, manufacturers can analyze vast streams of data from sensors and devices, leading to process optimization as events unfold.
The ability to make quick adjustments in response to changing conditions is not just a convenience—it's a competitive advantage.
The benefits of AI-powered data analytics extend beyond mere efficiency. Here's a snapshot of the additional advantages:
- Increased accuracy in quality control
- Improved inventory management
- Enhanced supply chain optimization
- Better worker safety
- Greater energy efficiency
As AI technology evolves, the potential for innovative solutions to optimize production processes is boundless. The manufacturing industry, akin to a well-oiled machine, is poised to reap the rewards of this digital revolution.
Case Studies: Success Stories of AI Integration
The integration of AI in manufacturing has led to a plethora of success stories that underscore its transformative impact. Siemens AG is a prime example, where AI has been leveraged to enhance predictive maintenance, leading to significant efficiency gains. Similarly, companies like General Electric and Toyota have utilized AI to improve product quality and operational safety, while Boeing and Intel have seen reductions in costs and environmental footprints.
Real-time data analytics and AI-driven process optimization have been at the core of these success stories. By harnessing the power of AI, manufacturers are not only able to predict equipment failures but also optimize production workflows, resulting in a more streamlined and cost-effective operation.
- Siemens AG: Predictive maintenance and efficiency.
- General Electric: Product quality and safety enhancements.
- Toyota: Operational safety and quality improvements.
- Boeing: Cost reduction and production optimization.
- Intel: Environmental impact reduction and process efficiency.
The adoption of AI in manufacturing is not a distant future but a present reality, with tangible benefits that are reshaping the industry landscape.
Enhancing Production Efficiency with AI
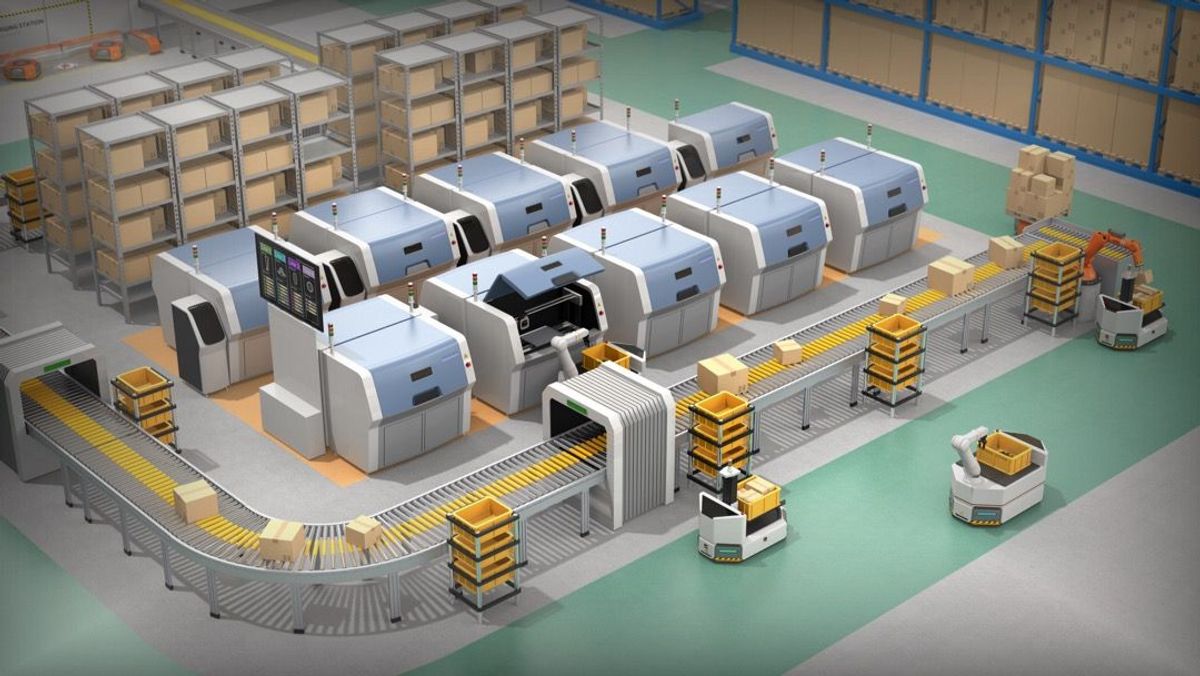
Automating Complex Tasks
The integration of artificial intelligence (AI) into manufacturing processes has been a game-changer for the industry. AI-enabled robots and cobots are now commonplace, working alongside human operators to perform complex tasks with unprecedented precision and agility. This collaboration not only enhances productivity but also fosters innovation within the manufacturing sector.
By automating complex tasks, manufacturers can significantly reduce the margin for error and increase the overall efficiency of production lines. This shift towards automation is not just about replacing human labor; it's about augmenting human capabilities and allowing the workforce to engage in more strategic and creative tasks.
The benefits of automating complex tasks with AI are manifold. Here's a brief overview:
- Reduction in manual errors
- Increased production speed
- Enhanced product consistency
- Improved worker safety
- Optimized resource utilization
The synergy between AI and industrial IoT, facilitated by smart factories, leverages extensive data streams to further optimize production processes. This strategic integration is at the heart of the modern manufacturing revolution, paving the way for a more efficient and innovative industry.
Streamlining Supply Chain Operations
In the realm of industrial goods, the integration of AI into supply chain operations has been a game-changer. AI-driven systems are now pivotal in orchestrating the complex dance of modern supply chains, ensuring that products are delivered efficiently and effectively to consumers and businesses globally. The use of AI in supply chain management, as highlighted by Deloitte, brings order to what was once a convoluted process, with a singular goal of seamless delivery.
AI has also proven instrumental in elevating productivity, reducing inventory expenses, and enhancing customer satisfaction through timely dispatch of goods. This multifaceted approach to supply chain administration not only addresses quality control and labor efficiency but also tackles the challenges of energy consumption, which impacts both costs and sustainability goals.
By predicting future product demands with high accuracy, AI enables companies to adjust production schedules and inventory levels accordingly. This foresight leads to reduced waste, lower costs, and improved delivery times, culminating in a supply chain that is both responsive and adaptable to market conditions.
Reducing Downtime through Predictive Maintenance
Predictive maintenance stands out as a transformative application of AI in manufacturing. By leveraging data from sensors on machinery, AI algorithms can detect early signs of wear and potential failures, enabling proactive maintenance actions. This approach not only minimizes unexpected downtime but also extends the lifespan of equipment and reduces maintenance costs.
Predictive maintenance strategies harness the power of AI to analyze sensor data and identify patterns that precede equipment failure. This allows for timely interventions, ensuring that maintenance is performed only when necessary, thus optimizing resource allocation.
The implementation of predictive maintenance can be broken down into several key steps:
- First Step in AI-Based Predictive Maintenance: Utilize IoT and data-driven solutions to monitor machine health.
- Data Analysis: Employ advanced analytics to interpret the data collected from sensors.
- Maintenance Scheduling: Plan maintenance activities based on predictive insights to prevent unplanned outages.
- Continuous Improvement: Refine predictive models over time to enhance accuracy and efficiency.
Quality Control and Sustainability
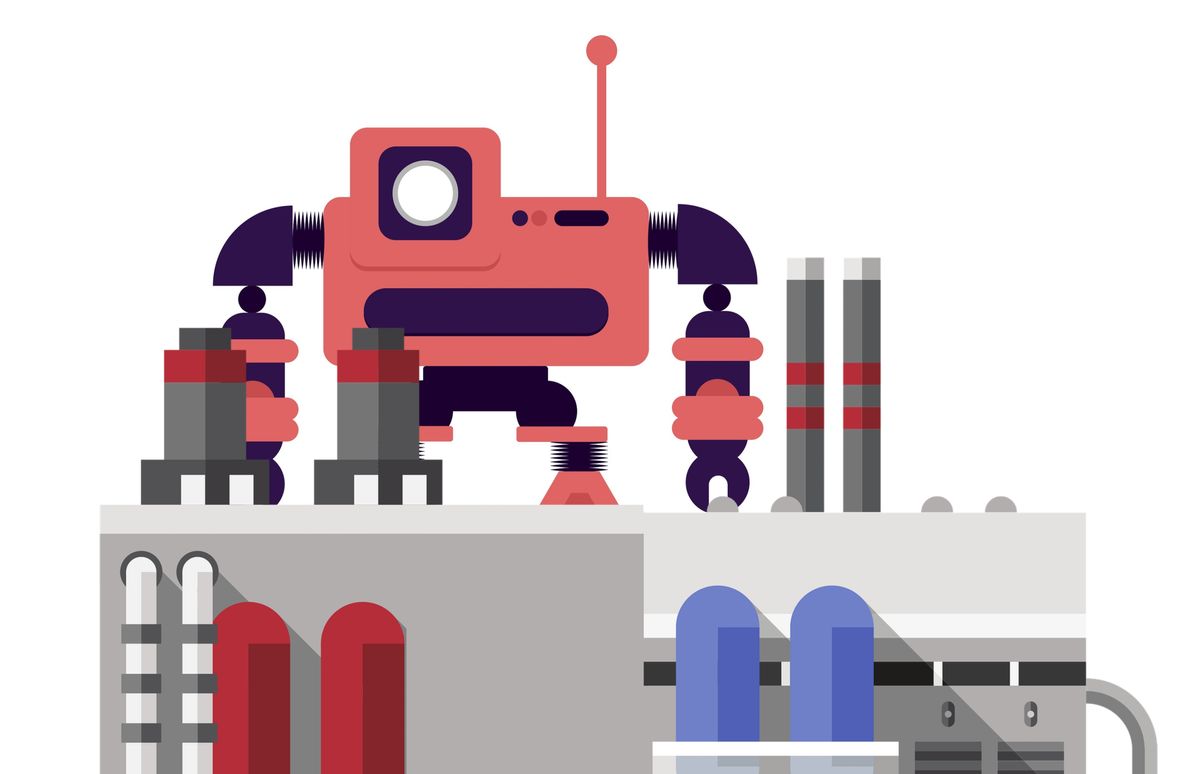
Improving Product Quality with Machine Learning
The integration of AI into manufacturing has ushered in a new era of quality control. Machine learning applications are now pivotal in detecting production defects with unprecedented precision. This not only minimizes errors but also significantly reduces waste. By analyzing data from various sources, such as sensors and cameras, machine learning algorithms can identify patterns indicative of potential issues.
The proactive use of machine learning for quality control ensures that manufacturers can maintain high standards while optimizing their production processes.
These advancements have led to a surge in efficiency, allowing businesses to produce goods at a lower cost without compromising on quality. As a result, manufacturers become more competitive in the market. The following list highlights key areas where machine learning has made an impact:
- Yield Optimization: Leveraging algorithms to enhance manufacturing data analysis and process refinement.
- Defect Detection: Utilizing AI-powered imaging for early identification of production flaws.
- Supply Chain Efficiency: Applying AI to predict demand and streamline inventory management.
Embracing AI not only boosts profitability margins through reduced operational costs but also positions manufacturers at the forefront of innovation. The commitment to technological advancement is a defining factor for success in the modern industrial landscape.
AI in Reducing Waste and Environmental Impact
The integration of AI into industrial goods manufacturing has marked a significant step towards sustainability. AI systems are pivotal in minimizing waste by optimizing production processes and reducing excess material use. By forecasting demand with greater precision, AI ensures that production is more aligned with market needs, thus avoiding overproduction and the resultant waste.
AI's role extends beyond the factory floor; it is also transforming waste management. For example, AI can enhance waste collection efficiency by optimizing routes and schedules based on real-time data. This not only improves operational efficiency but also contributes to a reduction in the carbon footprint of waste management services.
The strategic application of AI in manufacturing and waste management is a testament to its potential in driving environmental sustainability.
The following points highlight AI's impact on waste reduction:
- Streamlining supply chain operations to reduce excess inventory
- Implementing predictive maintenance to prevent resource wastage
- Utilizing precision agriculture techniques to optimize resource use in farming
By embracing AI, industries are not only achieving economic gains but are also playing a crucial role in protecting the environment.
Ensuring Consistency and Compliance
In the realm of industrial goods, the application of AI is pivotal for maintaining consistency and ensuring compliance with various industry standards. AI systems are instrumental in automating quality checks, which not only guarantees uniform product quality across high production volumes but also allows human workers to concentrate on more intricate tasks.
The integration of AI into quality control processes aligns with the broader objectives of Industry 4.0, which emphasize the adaptation of standards to revolutionize manufacturing with efficiency, quality control, and supply chain optimization. However, this technological integration is not without its challenges, such as ensuring data security and enhancing the workforce's skills to keep pace with AI advancements.
By leveraging AI for compliance, manufacturers can systematically address issues related to supply chain administration, energy consumption, and labor efficiency, thereby mitigating risks and fostering a culture of continuous improvement.
The following points highlight the impact of AI on consistency and compliance in manufacturing:
- Automated defect detection and quality control measures.
- Streamlined supply chain operations to minimize disruptions.
- Optimized energy consumption for cost-effective and sustainable production.
- Enhanced labor efficiency while prioritizing safety and high product quality.
AI-Driven Innovation in Product Development

Accelerating Design and Prototyping
The integration of AI into the design and prototyping phase is a game-changer for manufacturers. Virtual prototyping and design optimization are key components of AI's capabilities, allowing for cost-effective modeling and testing in virtual environments. This not only speeds up the development process but also slashes costs, ushering in a new era of product creation.
Generative AI (GAI) is particularly transformative, offering:
- Several layout options
- Streamlined transition from concept to prototype
GAI automates market research and predictive analysis, providing deep insights into consumer preferences and forecasting feature success. This ensures that products enter the market with a distinct competitive advantage.
Moreover, GAI can significantly reduce the time spent on coding activities, enhancing efficiency and creativity in product development. The impact of AI-driven innovation is especially notable in sectors like the automotive industry, where it revolutionizes vehicle design and manufacturing, enhancing efficiency, precision, and quality through robotics and machine learning.
By leveraging AI, businesses can harness the power of data to generate fresh ideas for products that resonate with consumer needs and preferences, while also accelerating the journey from concept to prototype.
Customization and Personalization through AI
The integration of AI into product development has ushered in a new era of customization and personalization, allowing manufacturers to cater to individual customer preferences with unprecedented precision. AI algorithms are pivotal in learning from customer feedback, enabling the creation of products that not only meet but often exceed consumer expectations. This capability is not limited to luxury items but extends across various sectors, including automotive, where AI revolutionizes the industry with personalized customer experiences.
In the realm of fashion and retail, AI's impact is particularly noticeable. Generative algorithms are at the forefront, analyzing trends and consumer data to produce unique designs. This innovation leads to a more personalized shopping experience, fostering customer satisfaction and loyalty. The benefits of AI in customization include:
- Personalized Experiences: Tailoring product features and designs to individual needs.
- Streamlined Processes: Automating market research and data analysis to enhance efficiency.
- Early Problem Detection: Identifying design issues early to prevent costly corrections later.
AI's role in personalization is not just about enhancing the consumer experience; it's also about driving efficiency and success in manufacturing. By offering recommendations and suggestions, AI helps online stores elevate the user experience, while technologies like virtual try-on booths and voice recognition further refine the shopping journey.
Fostering a Culture of Continuous Improvement
In the realm of industrial goods, the integration of AI is not just about the immediate enhancements it brings to manufacturing processes. It's about instilling a mindset of perpetual growth and development. AI serves as the catalyst for continuous improvement, driving companies to constantly refine their operations and products.
AI revolutionizes manufacturing with its ability to learn and adapt, creating a dynamic environment where innovation thrives. This is evident in the way AI contributes to various aspects of the industry:
- Quality Control: Ensuring the highest quality in the rapidly increasing production volumes.
- Supply Chain Administration: Overseeing a multifaceted worldwide supply chain to prevent interruptions and sustain operational effectiveness.
- Energy Consumption: High energy usage in manufacturing processes impacts costs and sustainability goals.
- Labor Efficiency: Optimizing labor in manufacturing processes while ensuring safety and high product quality.
By embedding AI into the core of their operations, organizations are not just reacting to changes but are proactively shaping their future. This proactive stance is crucial in maintaining competitiveness and achieving long-term success.
The commitment to continuous improvement through AI also extends to the workforce. The technology's role in employee empowerment has led to more innovative and secure working environments. For instance, Siemens' investment in AI has not only improved operational efficiency but also positioned the company as a leader in the digital transformation of manufacturing.
The Future of Manufacturing with AI
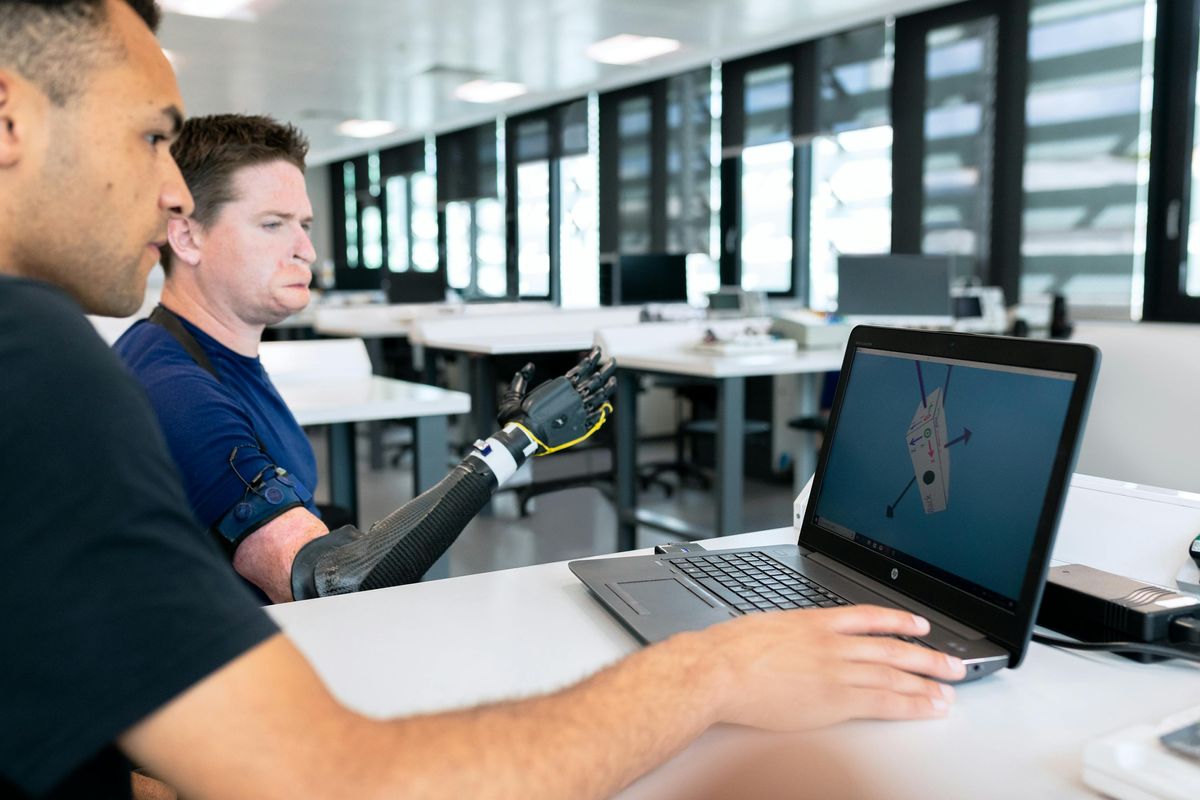
Predicting Trends and Adapting to Market Changes
In the rapidly evolving landscape of industrial manufacturing, the ability to anticipate market trends and swiftly adapt to changes is crucial. Integrating data from the equipment with other manufacturing process data has been a significant trend among manufacturers, enhancing their predictive capabilities. This integration allows for a holistic view of operations, enabling more accurate forecasts and strategic planning.
By harnessing the power of AI, companies can analyze vast amounts of data to gain deeper insights into consumer behavior, market trends, and product performance. These insights are instrumental in driving innovation and maintaining a competitive edge.
The use of machine learning algorithms has revolutionized decision-making in manufacturing. By analyzing data from various sources, such as sensors on machines and production lines, businesses can identify and address inefficiencies:
- Pinpointing bottlenecks
- Improving operational speed
- Ensuring high-quality standards
- Reducing production costs
As a result, manufacturers are not only able to keep up with market demands but also to lead the way in setting new industry standards.
The Evolution of Employment in the AI Era
The integration of AI into manufacturing is not just about technological advancement; it's about reshaping the workforce. AI in manufacturing revolutionizes equipment maintenance, production efficiency, and customization at scale, leading to cost savings and improved quality control. However, this transformation also brings forth challenges in employment dynamics.
While some roles may become obsolete, AI creates a surge in demand for new skill sets, particularly in data analysis and software programming. This shift necessitates a proactive approach to workforce development, ensuring that employees are equipped with the necessary skills to thrive in an AI-enhanced environment.
It is imperative for companies to not only invest in AI technologies but also in the human capital that will drive these innovations forward.
Ethical considerations are paramount as we navigate this new era. Companies must ensure that AI is used responsibly, preventing job displacement and avoiding the exacerbation of existing inequalities. The future of manufacturing with AI is not just about the machines; it's about the people who make them work.
Preparing for the Next Industrial Revolution
As we stand on the brink of the next industrial revolution, it is clear that artificial intelligence (AI) will be at the forefront, shaping the future of manufacturing. Embracing AI is essential for competitiveness in an industry that is increasingly driven by efficiency, quality improvement, and predictive maintenance. However, the journey towards AI integration is not without its challenges, such as data integration and workforce training.
To navigate this transition successfully, manufacturers must focus on several key areas:
- Developing robust strategies for AI implementation
- Investing in employee education and skill development
- Establishing partnerships for technological innovation
- Ensuring data security and privacy
The adoption of AI in manufacturing revolutionizes the industry, but it also requires a proactive approach to overcome obstacles and leverage opportunities for growth.
By addressing these challenges head-on and fostering a culture of continuous learning and adaptation, manufacturers can not only survive but thrive in the AI-driven landscape. The future of manufacturing with AI promises not just incremental changes but a complete transformation of how we produce, innovate, and meet the demands of a dynamic market.
Embracing the AI Revolution in Manufacturing
In conclusion, the integration of artificial intelligence into the manufacturing sector is not just a trend but a transformative movement reshaping the industry. AI's ability to enhance efficiency, reduce costs, and improve product quality is revolutionizing manufacturing processes, leading to the emergence of smart factories and innovative production methods. As we have seen through various case studies, industry leaders like Siemens, General Electric, Toyota, Boeing, and Intel are already reaping the benefits of AI, from predictive maintenance to intelligent automation. The future of manufacturing lies in the adoption of AI technologies, which promise to bring about a new era of efficiency, sustainability, and competitiveness. As the industry continues to evolve, it is clear that AI will play a pivotal role in driving innovation and maintaining the relevance of manufacturing in the global economy.
Frequently Asked Questions
How is AI enhancing efficiency in manufacturing?
AI is enhancing manufacturing efficiency by automating complex tasks, optimizing production processes, and enabling predictive maintenance. This reduces downtime, minimizes human error, and streamlines workflows, leading to increased productivity and reduced costs.
What are smart factories and how do they utilize AI?
Smart factories are advanced manufacturing facilities equipped with AI-powered sensors, machines, and systems. They utilize AI to collect and analyze real-time data, optimize operations, and improve product quality, resulting in more efficient and flexible production lines.
Can AI improve product quality in manufacturing?
Yes, AI can significantly improve product quality by employing machine learning algorithms to detect defects, ensure consistency, and adapt processes for better outcomes. This leads to higher-quality products and greater customer satisfaction.
What role does AI play in reducing waste and environmental impact in manufacturing?
AI plays a critical role in reducing waste by optimizing resource usage and production processes. It enables manufacturers to forecast demand more accurately, minimize overproduction, and efficiently manage supply chains, which collectively reduce environmental impact.
How does AI contribute to innovation in product development?
AI contributes to innovation by accelerating design and prototyping, offering customization options, and enabling continuous improvement through data analysis. This allows manufacturers to rapidly develop new products and tailor them to specific customer needs.
What is the future of employment in manufacturing with the rise of AI?
The rise of AI in manufacturing is leading to an evolution of employment, where the demand for traditional manual skills may decrease, but there is an increasing need for AI literacy and technical skills to manage, maintain, and work alongside AI systems.